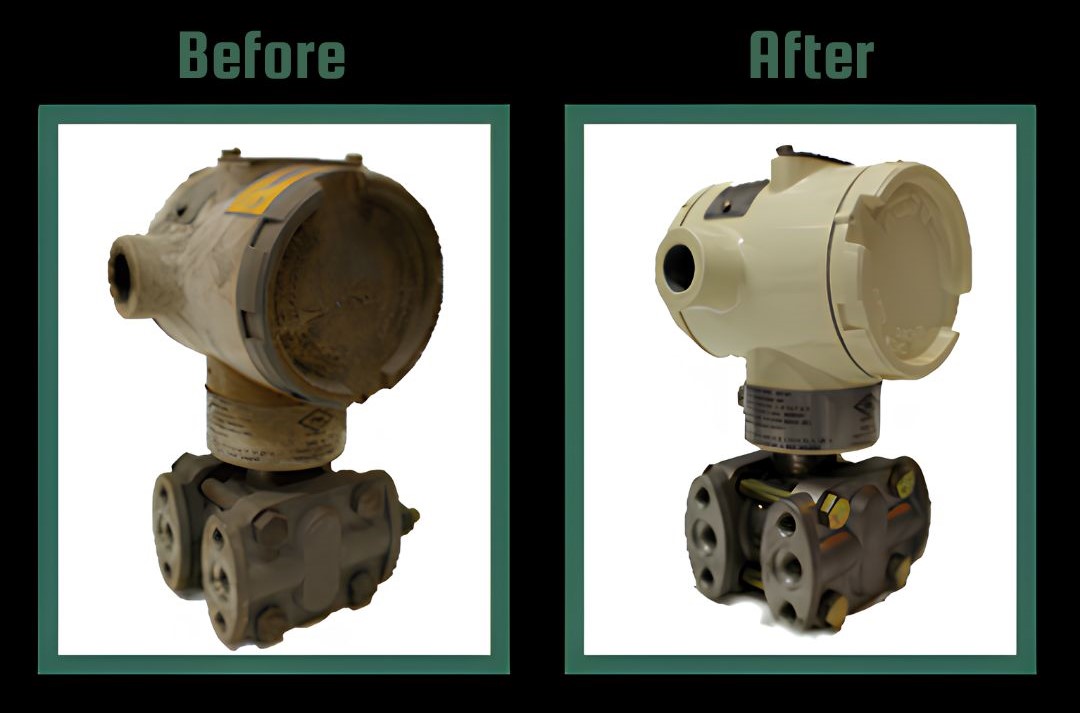
Precision Cleaning for Critical Services
Chlorine Cleaning Process
At Haygor, we specialize in thorough cleaning manifolds, valves, flowmeters, fittings, transmitters, gauges, and other instruments used in chlorine service applications. Our meticulous cleaning process begins by disassembling parts and isolating any components incompatible with our cleaning solutions. The remaining parts undergo an initial pre-cleaning stage, which may include grinding, wire brushing, blasting, or swabbing to remove surface contaminants.
Each component is then cleaned with EnSolv®, ensuring the complete removal of any residual impurities. Depending on the need, we accelerate drying using dry nitrogen before proceeding with a rigorous inspection.
Chlorine Cleaning Inspection & Finalization
Once cleaned, every part is subjected to a dual-stage inspection process. First, a strong white light examination identifies any moisture, grease, oil, or lint. If a component clears this stage, it moves to a blacklight inspection in a controlled environment to detect any invisible contaminants, such as smears or residue. Any part that does not pass is re-cleaned until it meets our strict standards.
For lubrication, Fluorolube GR290 is applied unless specified otherwise. Approved components are labeled “Cleaned for Chlorine Service”, securely bagged, and sealed. If reassembly is required, we ensure proper testing and calibration before finalizing the equipment. Any post-assembly work is flushed with EnSolv, followed by an oil-free air or nitrogen drying process. Flushing fluid is closely inspected to confirm cleanliness before sealing the unit.
Decades of Experience in Chlorine Cleaning
Haygor has been a trusted partner in the Petrochemical industry for over 30 years, delivering expert-level critical cleaning. Our team has over 50 years of combined industry experience, handling both legacy and modern industrial instruments. With state-of-the-art equipment and a specialized powder coating process, we ensure a durable and reliable finish for remanufactured components.
Ethylene Oxide (EtO) Cleaning for Specialized Equipment
Some equipment—such as medical and pharmaceutical devices—cannot withstand traditional high-temperature steam sterilization. For these, Ethylene Oxide (EtO) Sterilization provides a highly effective alternative. This process is ideal for items containing electronic components, plastic packaging, or delicate materials that could be damaged by conventional methods.
EtO Sterilization Process
Haygor follows a structured three-phase approach to ensure proper sterilization:
- Pre-Conditioning – The batch load is placed in a temperature- and humidity-controlled environment, allowing microbial growth to reach an optimal phase before sterilization.
- Sterilization Phase – The batch undergoes an extended sterilization cycle, which includes:
- Temperature and pressure control
- Vacuum testing and leak-rate analysis
- Multiple gas flushing cycles
- Dynamic Environmental Conditioning (DEC)
- EtO gas injection followed by a sterilization dwell period
- Post-cycle vacuum drying and initial washing
- Degassing Phase – To ensure all sterilized components are completely free of EtO residue, they undergo a controlled degassing process in a temperature-regulated chamber before release.
Why Choose Haygor for EtO Cleaning?
EtO sterilization is a highly controlled, complex procedure, requiring precision and expertise. With 30+ years in the Petrochemical industry and a team with over 50 years of experience, Haygor provides the technical knowledge and advanced equipment needed to ensure your sensitive products are properly sterilized.
Oxygen Cleaning Services
For oxygen service equipment, cleanliness is more than just a requirement—it’s a safety necessity. Contaminants like oil, grease, or residue can lead to fire or explosion hazards, making professional cleaning a critical step in equipment maintenance.
Oxygen Cleaning Procedure
Haygor's oxygen cleaning process ensures every component meets the highest safety and performance standards:
- Disassembly & Compatibility Check – We separate any parts that are incompatible with our cleaning agents before proceeding.
- Pre-Cleaning – Components undergo grinding, wire brushing, blasting, or swabbing to remove surface contaminants.
- EnSolv® Cleaning & Drying – Parts are cleaned with EnSolv®, then dried using oil-free air or nitrogen.
- Comprehensive Inspection –
- White light examination detects moisture, grease, or lint.
- Blacklight inspection identifies hidden contamination like smears or residues.
- Any part failing inspection is re-cleaned until it meets our quality standards.
- Final Assembly & Testing – Approved parts are labeled “Cleaned for Oxygen Service”, sealed, and, if applicable, reassembled, tested, and calibrated.
A Trusted Name in Oxygen Service Cleaning
With decades of experience in industrial cleaning, Haygor understands the risks associated with improperly cleaned oxygen equipment. Our team’s expertise, precision, and advanced cleaning methods ensure that every component meets stringent industry safety requirements.
Why Haygor?
- 30+ years of industry expertise
- 50+ years of combined team experience
- Advanced state-of-the-art cleaning processes
- Strict quality control and inspection protocols
- Commitment to safety, reliability, and performance
For industry-leading critical service cleaning, trust Haygor Instrument to deliver precision, expertise, and proven results.