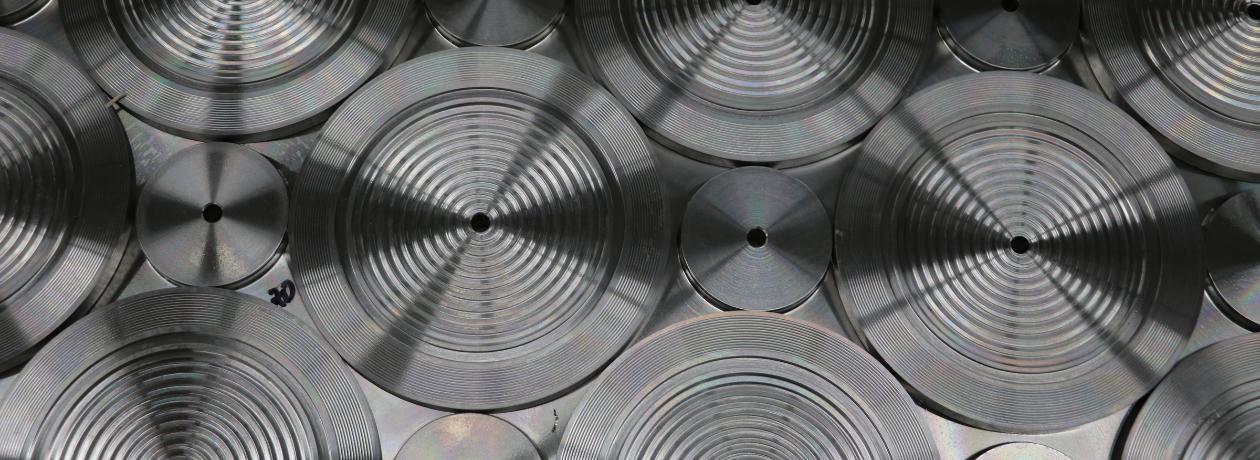
What is a Diaphragm Seal and When Should You Use One?
In industrial process environments where accuracy, durability, and safety are essential, diaphragm seals are often the unsung heroes of instrumentation. Whether you’re in refining, food and beverage, chemical production, or energy, chances are your instruments are exposed to conditions that could shorten their lifespan or compromise their performance.
In this blog, Haygor's Global Director, Stephen Tennis II, a leading authority on diaphragm seal systems, shares in-depth insights into what diaphragm seals are, how they work, why they matter, and what makes Haygor’s approach to customization and innovation stand out in today’s industrial market.
What Is a Diaphragm Seal?
A diaphragm seal, also known as a chemical seal, is a mechanical device that isolates a pressure-sensing instrument from the process media it is monitoring. It transfers pressure through a hydraulic system to the instrument, allowing it to take accurate measurements without ever coming into direct contact with potentially harmful or corrosive substances.
Stephen puts it best:
“It kind of works just like the brakes on your car. When the process presses on the diaphragm, that pressure gets transferred hydraulically to the instrument. The instrument sees the pressure—but never touches the process.”
This analogy is perfect. Just as your car's brake system uses fluid to transmit force from your foot to the brakes, diaphragm seals use a fill fluid to relay pressure from the diaphragm to the instrument, ensuring no direct contact with hot, corrosive, or clogging process fluids.
Why Are Diaphragm Seals Necessary?
Instruments are only as reliable as the environment allows. When gauges, transmitters, switches, or controllers are exposed directly to process conditions, especially those that involve high heat, vibration, or corrosive materials, their lifespan and accuracy can suffer significantly.
Key reasons to use diaphragm seals include:
-
Temperature Isolation: Instruments are calibrated at room temperature (about 72°F). When exposed to process temperatures that soar past 212°F (100°C), measurement accuracy can decline drastically.
-
Chemical Compatibility: Instruments are typically built with limited material options (brass, stainless steel, Monel, and Hastelloy). If your process involves more aggressive chemicals, diaphragm seals can be made from specialized materials like tantalum, titanium, zirconium, or even gold-plated alloys to significantly reduce corrosion.
-
Protection from Mechanical Stress: Vibration, pulsation, and crystallization from the process can physically damage an instrument. Diaphragm seals serve as a protective buffer.
-
Compliance with Sanitary Regulations: In industries like food, beverage, and pharmaceuticals, diaphragm seals help ensure hygienic design by eliminating crevices where bacteria could grow.
-
Enhanced Safety: By remote mounting instruments, technicians can safely read measurements without exposing themselves to hazardous or difficult-to-access locations.
The Seven “Killers” of Pressure Instruments and How Diaphragm Seals Help
Stephen outlined what he calls the “seven major killers” of pressure instruments, and diaphragm seals are designed to combat each one:
-
Temperature Extremes
Instruments experience drift and inaccuracy at elevated temperatures. Every 18°F above calibration temperature results in a 0.3% loss of full span accuracy, on top of the base error. Diaphragm seals insulate the instrument from the heat and can be paired with specialized fill fluids to mitigate thermal expansion issues. -
Chemical Incompatibility
Process media that interact negatively with the instrument's internal components can cause rapid corrosion. Diaphragm seals offer material flexibility that instruments alone don’t, allowing for highly resistant alloys or coatings like PTFE, gold, or platinum. -
Vibration and Pulsation
Common in systems with pumps or motors, these forces can cause rapid wear and premature failure. A diaphragm seal absorbs and isolates those forces before they reach the instrument. -
Crystallization
Media that change from liquid to solid, like sugars or waxes, can crystallize inside the instrument and clog it. The seal ensures that transformation happens outside the instrument housing. -
Clogging
Small orifices inside instruments are easily blocked by viscous or particulate-laden fluids. Diaphragm seals with flush connections eliminate this risk. -
Sanitary Considerations
In regulated industries, hygiene is critical. Seals designed to eliminate dead space and withstand sterilization (e.g., steam cleaning) are standard in food-grade applications. -
Technician Safety and Accessibility
Diaphragm seals allow remote mounting of instruments, minimizing technician exposure to heat, chemicals, or hazardous locations.
How Do You Know If You Need a Diaphragm Seal?
If your instruments are failing prematurely, showing poor accuracy, or needing constant maintenance, it may be time to consider a diaphragm seal. Often, users will replace a failing gauge or transmitter with the same model, without considering whether the process conditions are to blame.
Stephen explains:
“If you’re not getting the life you want out of your instrument, it’s not just about replacing it. There’s probably something in your process that’s degrading the equipment. That’s when a diaphragm seal can make a huge difference.”
Haygor’s Customization and Rebuild Services: What Sets Us Apart
At Haygor Instrument and Company, Inc., diaphragm seals aren’t a sideline, they’re the main event. Unlike competitors who are tied to a specific brand of instruments, Haygor operates independently, allowing us to provide diaphragm seals for any instrument, from any manufacturer.
Here’s what makes Haygor different:
-
Broad Compatibility: We support gauges, transmitters, switches, and controllers across all brands.
-
Rapid Customization: We develop and deliver custom products in days, not months or years.
-
Innovation Leadership: Proprietary solutions like the Thermal Guardian and Temperature Compensating Remote Seal System tackle problems no one else is addressing.
-
High Volume, Fast Turnaround: We maintain a massive inventory of parts, ensuring lead times as short as 1–5 days.
-
Engineering-Driven Approach: Every diaphragm seal is part of a precision-engineered system, not just an add-on.
Cost and Long-Term Savings
While adding a diaphragm seal may slightly increase upfront cost, the long-term savings are substantial:
-
Extended Equipment Life – Multiply the lifespan of your instruments, reducing replacement frequency.
-
Reduced Downtime – Less maintenance and fewer unexpected failures mean improved productivity.
-
Improved Safety – Fewer technician interventions in dangerous areas reduces risk and liability.
-
Lower Operational Costs – Decrease the frequency of recalibration and minimize process disruptions.
Additionally, Haygor offers repair services to extend the life of your equipment even further. Our team can replace worn seals, recalibrate, and return your instrument with a new warranty, saving both time and capital investment.
Material Selection, Fill Fluids, and Design Flexibility
Choosing the right diaphragm seal involves more than just ordering a part, it requires a careful look at your process conditions, media characteristics, and measurement requirements.
At Haygor, we offer:
-
Over 25 Fill Fluids – Tailored for temperature range, viscosity, and media compatibility.
-
Custom Thicknesses and Sizes – From 0.6” to 4.1” and everything in between.
-
Exotic Materials and Coatings – Gold-plated, PTFE-coated, titanium, zirconium, and more.
-
Advanced Sizing Tools – Our internal performance calculator helps us determine the ideal diaphragm diameter and fill volume for your specific application.
Key Industries That Rely on Diaphragm Seals
While diaphragm seals can be found across a wide array of sectors, they’re especially critical in:
-
Downstream Oil & Gas (Refining)
-
Chemical and Petrochemical
-
Food and Beverage
-
Pulp and Paper
-
Hydrogen and Clean Energy
-
Nuclear
-
Cannabis and Nutraceuticals
Remote mounting, chemical resistance, and hygiene requirements make diaphragm seals indispensable in these high-demand settings.
Final Thoughts: Your Partner in Process Measurement Protection
Diaphragm seals are not just accessories, they're essential components in achieving reliable, long-lasting, and safe pressure measurement. At Haygor Instrument and Company, Inc., we don't just sell products, we help you solve problems.
Whether you're upgrading legacy systems, troubleshooting instrument failures, or designing for a new facility, our expert team is here to help. From consultation to customization to ongoing support, Haygor is committed to being your go-to resource for diaphragm seal solutions.
Need support or have a diaphragm seal challenge?
Contact Haygor Instrument and Company Inc. today and speak with one of our diaphragm seal specialists. Let us help you protect your instruments, and your bottom line.